

The value of non-contact air bearings has enormous advantages over mechanical and magnetic solutions. The air bearing is used as standard solution in the Turbo Blowers of the AT and TB Series. Hence, this is why AERZEN relies on another system.ĪERZEN uses air for Non-Contact bearing system Overall, the solution by magnetic bearings is more expensive over the long term, technically overcomplicated, and energy inefficient. The battery packs must be regularly checked using a special maintenance plan, and replaced when there are damaged or older/weaker battery cells. Because the installed batteries must be fully charged and stabilised, a UPS also requires its own maintenance. The UPS can also be switched off, only after the speed decreases to a safer and manageable level. The workload on the emergency bearing would be so great at full-speed, costly damages would be highly likely. The so-called UPS (Uninterruptible Power Supply) ensures that the high-frequency rotating rotor does not immediately come across the mechanical emergency bearing when the power supply fails. Additionally, a backup battery must be provided for an emergency, in case of an interruption of the power supply. Regarding the balance of power, the magnetic bearing is not ideal, because a constant production of power is required for the generation of the magnetic field which increases the turbocharger’s operating costs. This means, in addition to planning the logistics of it all, a critical and possible three-month waiting period for the machine. If something needs to be repaired or replaced, it cannot be done at the installation site only at the manufacturer. One of the most significant drawbacks is the very limited service possibilities. This results in a frequent failure of the turbomachinery on many systems. Due to their complex control circuit, magnetic bearings are rather more limited with regard to robustness, and are quickly switched-off in extreme situations. Additionally, there is high sensitivity in operating and processing pressure fluctuations and peaks, and technologic aspects such as the compressor pump.įor both, dynamic forces that work on the rotor of the machine are created. On the other hand, the complex controls require regular maintenance. On one hand, certain environmental conditions are often not ideal for sensitive components especially in sewage treatment plants. The use of finely calibrated sensors and the overall complex control circuit also has disadvantages. Only then, can the electric currents adjust the magnetic fields as precisely as necessary, for trouble-free continuous operation. To ensure a smooth function, the system must constantly check the exact position of the shaft. This solution is highly complex, and the implementation is also quite technically complex. This type of bearing generates corresponding magnetic fields into the interior of the blower, completely avoiding contact between the fast-rotating shafts and other components. Previously and for the longest time, magnetic bearings were the most practical solution. Therefore, modern speed-controlled turbos are also referred to as "oil-free" high-frequency Turbo Compressors.

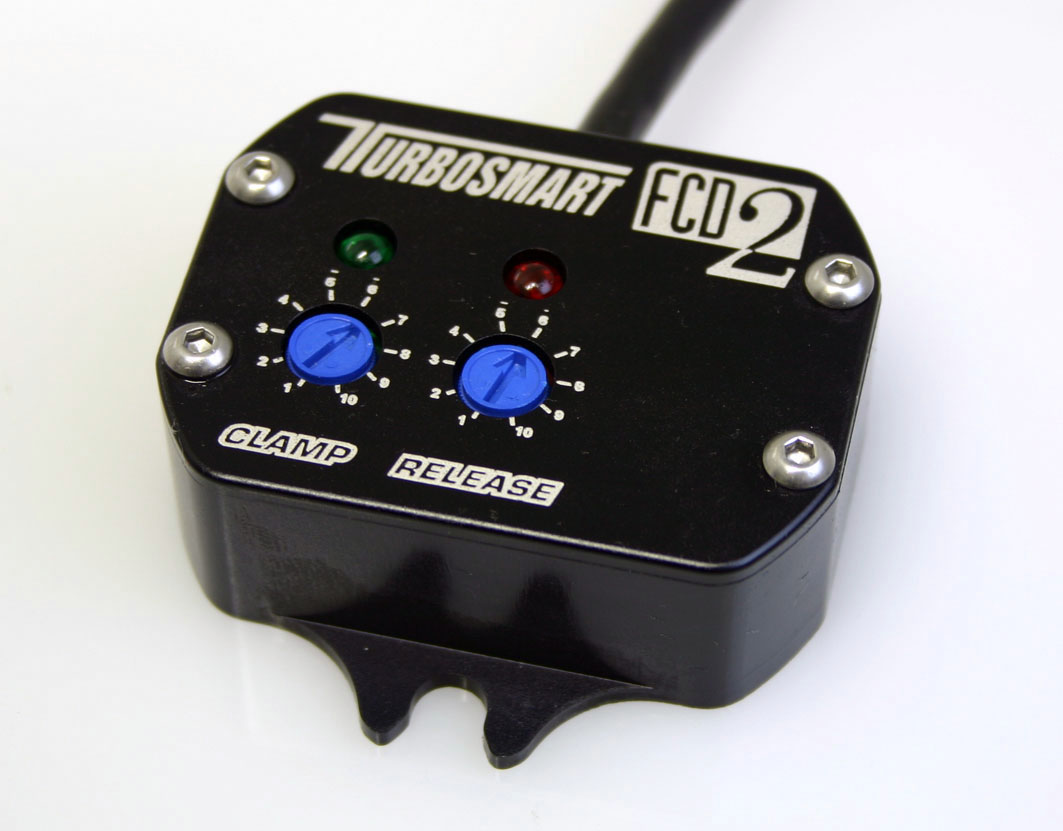
The non-contact bearing also eliminates unnecessary maintenance like lubrication (e.g.: Oil). In principle, there are two approaches for the implementation of a friction-free and non-contact bearing of Turbochargers: Magnetic bearing and air bearing. Solutions for smooth bearing system of the Turbo Compressors - Magnetic bearings or air bearings Ergo, turbomachines in sewage applications require bearings that operate without mechanical friction, and ensure a smooth operation of the turbocharger during the compression process. In this case, "frictionless" is known within the context of contemporary innovation since conventional ball bearings or other mechanical bearings, which always cause some amount of friction are not practical at the high-rotational speeds, generated inside a turbo blower. To enter the necessary oxygen into a basin, the flow machines must function smoothly in a harsh environment over long periods of time. The more efficient the aeration, the better. The air supplies the microorganisms into the basin with oxygen. Turbomachines particularly must do their jobs without major interruptions due to maintenance and repairs - they boost air into the aeration tanks. Reliability, energy efficiency, and reduced maintenance costs are extremely important. Turbo blowers and/or turbo compressors are extensively used in sewage treatment. AERZEN Turbo Blower for Wastewater applications
